

These discs were placed in a kiln to strengthen and then cooled to remove the stresses built up during manufacture. The globe was then reheated and rotated at considerable speed, causing it to be spun out into a flat disc or ‘table', about five feet in diameter.
BLUE REFLECTION SECOND LIGHT GLASS SHEET CRACK
When it was the right size an iron rod called a ‘pontil' or ‘punty' was attached at the base of the globe to crack it from the blowpipe. In this process the glass maker gathered molten glass on the end of a blow pipe, and then formed it into a globe by reheating, rotating and blowing. It was a highly skilled process producing a superior quality product. From 1700 to 1840, it was the main method of manufacture. Glass made in this way had a rough surface and was not always transparent.Ĭrown glass was introduced to London from France in 1678. The two ends are cut off and the cylinder that is left is split with shears while still hot and flattened out on an iron plate. The process involves gathering molten glass onto a ‘blowpipe’ and then creating an elongated balloon shape. The glass is fitted using putty which is then painted to blend with the surrounding joinery.īroad sheet glass was first made in Sussex in 1226, but was of poor quality and fairly opaque. The glazier fits the panes of glass to the window frame, usually before the window is installed within the building. Additionally, by this period it was possible to manufacture glass plate, a process undertaken by the British Cast Plate Glass Company who, in 1789, began using a machine powered by steam to grind and polish plate glass for use in mirrors, coaches and the homes of the extremely wealthy. The third challenge has been to develop technologies that would produce large, clear, glass sheet.Ībove: Stained glass window in the hall of 13 Brunswick Square.īy the Regency several methods were known for making glass for glazing, including cylinder glass, broad sheet glass and crown glass technologies. A recipe from the 1770s used flint ‘glass’, purified pot ash and red lead, whilst one from the 1830s recommended six molecular parts of silica and one part each of sodium, calcium and magnesium oxides. A second major challenge has been the identification of appropriate fluxes with which to melt silica at achievable temperatures. Just one gram of iron oxide in a ton of silica will give the glass a green tint.
BLUE REFLECTION SECOND LIGHT GLASS SHEET FREE
One of the recurring themes in the history of glass has been the search for sources of sand that are free of contaminating oxides.
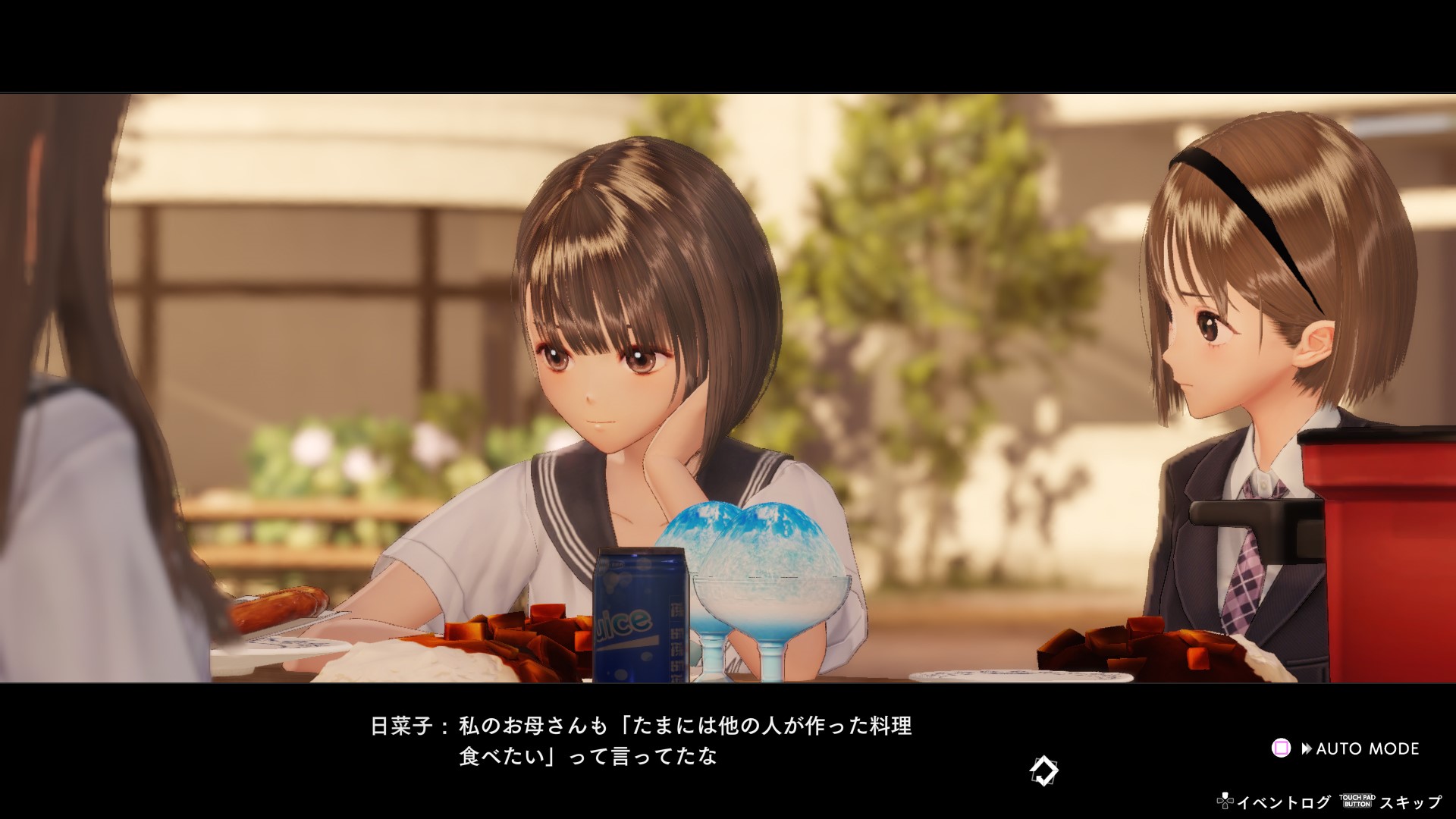
The principle ingredient for the manufacture of glass is silica, the most common source of which is sand.
